2021年,隆重庆祝中国共产党成立100周年之际,石油化工研究院也迎来建院15周年。
15年栉风沐雨,书写奋斗华章,以科技创新引领高质量发展之路。
15年凯歌高奏,奋进世界一流,以如磐初心铸就中国石油炼化科技之光!
15年来,在集团公司党组的正确领导下,石化院坚持“一部三中心”发展定位和五个紧密结合工作方针,砥砺前行、奋勇拼搏,以“八个坚持”为基本遵循,以“六种意识”为思想保障,以“八个转变”为改革抓手,以“六个一流”为发展目标,坚持科技与管理创新“双轮驱动”,在炼化新技术、新产品开发、成果推广、人才队伍、党的建设等各方面都取得了显著成绩,实现了从无到有、从小到大、从弱到强的跨越式发展,成为集团公司炼化科技创新主力军。
自主开发的新技术、新产品在国内外50余家企业的170余套工业装置推广应用,创效30亿元以上。荣获省部级以上科技奖励394项,其中国家科技进步一等奖1项、二等奖7项,中国专利金奖1项。集团公司科技进步特等奖3项,基础研究一等奖2项,技术发明(创新)一等奖6项,科技进步一等奖31项。申请专利3552件,授权1948件,其中发明专利1617件,占83%。认定技术秘密563项。“十三五”期间,制修订ISO国际标准11项,占集团公司的47%;合成橡胶创新团队荣获集团公司“科技创新团队”称号。在集团公司年度业绩考核中,石化院连续3年获得A级,近两年科研板块排名第一。
科研实力持续提升。坚持实施“优势领域保持领先、攻关领域跨越式发展、储备领域占领制高点”创新工程,持续开展科研项目顶层设计,明确科研战略发展路线图。炼油主体系列催化剂研发成功并得到全面推广应用,化工重点催化剂研发及化工新产品研发取得重要成果。近5年来,牵头承担润滑油、合成橡胶两个国家项目和6个公司重大科技专项,完成40余项重大工业试验,成功竞聘集团公司炼化领域全部7项关键核心技术项目。面对突发新冠肺炎疫情,以最短时间、最快速度、超常规手段,完成熔喷料熔喷布自主研发生产,助力快速打通“熔喷料—熔喷布—口罩”全产业链。
科研平台日臻完善。以高端化、智能化平台建设为支撑,夯实高质量发展基础。合作建设1个国家重点实验室,建成4个行业重点实验室、5个集团公司重点实验室和5个中试基地,4个检验中心全部获得CMA/CNAS双认证,搭建了包括超过1000台套重要试验装置设备在内的国际一流研发平台。作为唯一的科研单位,入选集团公司数字化转型智能化发展首批11家试点,围绕智慧科研、智能实验室、智慧服务3条业务主线,谱写“智慧研究院”建设新篇章。
人才强院支撑发展。实施“人才强院”工程,开展领导干部、青年英才、科研骨干等赋能培训,培养和造就一批具有国际水平的战略科技人才、科技领军人才、青年科技人才。聚焦炼化转型升级,建立市场化引才新机制,先后引进两名国家特聘专家,引进两名院士建立院士工作室,选派14名优秀青年骨干赴法国IFP研修培训。配套制定科研创效专项奖励政策,完成首届“双序列”专家评聘,畅通人才职业发展通道,为科研人才赋能放权。
深化改革激发活力。厘清行政和科研管理权责分配,全方位深化改革,全力释放发展动能。以领军人才为核心,推进跨领域、多学科联合攻关的创新团队建设,赋予创新团队负责人“团队组建权、技术内容决策权、经费使用审批权、绩效考核激励权”,组建5个院级创新团队和若干室级创新团队。积极识变应变,开展炼化碳达峰碳中和对策研究,氢能、生物化工、新材料等新领域创新工作全面展开。
对外合作互惠共赢。打造“没有围墙的研究院”,与国内一流院所及行业龙头企业建立联合实验室6个,与8家企业建立“框架协议+合同”合作模式,与工程院成立首个上下游“创新联合体”,打通技术研发到成果转化最后1公里,形成利益共同体、命运共同体。主动带入全球科技创新网络,加强与埃克森美孚等国际知名公司开展低碳排放等合作项目11项,举办高端国际论坛16个,积极推动炼化优势特色技术及产品“走出去”。
企业文化凝心聚力。大力弘扬大庆精神铁人精神和科学家精神,把诚实守信打造成石化院人的“金字招牌”。全院“共做一课题”,千人一心谋发展,形成了学习日、创新讲堂、读书实践等文化品牌。发挥先进典型示范引领作用,连续两届获“首都文明单位”,获中央企业青年创新奖和青年文明号等国家、省部级先进集体20余个,获得中央企业劳动模范、集团公司劳动模范等先进个人380余人次。一年一个主题,持续开展科研基础技能竞赛,群众性文体活动丰富多彩,文化引领力、感召力、凝聚力不断增强。关心关爱员工,积极为员工办实事解难题,凝聚发展正能量。
党建引领阔步前行。发挥党委把方向、管大局、保落实领导作用,坚决贯彻“两个一以贯之”,持续推进从严治党,以高质量党建引领高质量发展。充分发挥党支部战斗堡垒作用,围绕科研抓党建、抓好党建促科研,以“党建元素+支部特色+发展创新”为平台,创建石化院党建品牌,推动党建与科研深度融合,促进党建科研双丰收。充分发挥党员在科研攻关中的模范带头作用,广大党员在“学术诚信、科研创新、勤奋学习、遵规守纪、团结协作、践行石油精神、服务奉献、推进改革”8个方面当先锋、做表率,有30多个先进基层党组织、50多名优秀共产党员和党务工作者受到集团公司以上表彰,特别是重油加工室党支部,荣获中央企业“先进基层党组织”、集团公司党建“百面红旗”称号。
围绕“支撑和引领炼化业务转型升级,打造世界一流”的目标,坚定企业研究院属性,每年设立“1号工程”,一年一主题、一年一重点,以自主创新筑牢自立自强之基,为炼化转型升级提供技术利器,有力提升了炼化科技硬实力。
自主创新技术 覆盖85%以上炼油过程
今年6月,自主研发的连续重整催化剂在乌石化成功应用,标志着中国石油实现炼油主体系列催化剂技术全覆盖。
●汽油质量升级成套技术:成功研发出由催化汽油选择性加氢脱硫、催化汽油加氢脱硫—改质、轻汽油醚化等成套技术,在20余家企业应用,总加工能力1300万吨/年,为中国石油汽油质量升级作出重要贡献。
●柴油质量升级成套技术:形成了柴油加氢精制、加氢改质和异构降凝系列成套技术,3大系列10个牌号催化剂先后在15套工业装置应用,加工能力2380万吨/年。单反应器柴油加氢精制裂化组合催化剂首次工业试验取得成功,炼化转型升级又添自主技术利器。
●催化裂化催化剂:开发出Y型分子筛、ZSM-5择形分子筛等18种催化新材料,形成了清洁汽油组分生产、抗重金属等6大系列57个牌号催化剂。在80余套装置应用,内部市场占有率70%。在雪佛龙美国炼厂、埃克森美孚澳大利亚炼厂等14个国家和地区的17套装置应用。
●渣油加氢催化剂:开发出脱金属剂、脱硫剂、脱残炭剂和保护剂4大类12个牌号PHR系列渣油加氢催化剂,先后在大连西太、大连石化两家企业3次应用,今年7月在中国台湾中油公司成功应用。
●加氢裂化催化剂:中油型、化工原料型加氢裂化催化剂在大庆石化120万吨/年装置上应用,劣质柴油加氢裂化催化剂在抚顺石化120万吨/年装置上应用,为集团公司多产化工原料提供技术支持。
●催化轻汽油醚化技术:可降低催化汽油的烯烃含量和蒸气压,提高辛烷值,并将低价值甲醇转化为高价值汽油组分,是提升汽油质量的补充技术。先后建成投产10余套催化轻汽油醚化装置,最大规模为50万吨/年。
●润滑油加氢催化剂:牵头承担国家重点项目“高性能润滑油生产关键技术攻关及应用”,开发了加氢精制—异构脱蜡—补充精制润滑油基础油生产成套技术,3次在大庆炼化工业应用,解决了高含蜡原料生产高黏指重质基础油难题。
●石蜡加氢催化剂:开发了SD-1、SD-2石蜡加氢催化剂,可生产满足美国FDA标准的食品级石蜡、微晶蜡,已在工业装置应用10余次,内部市场占有率57%。
●航煤加氢催化剂:性能指标满足3号航煤国家标准,通过优化工艺,控制物耗、能耗,催化剂加氢活性高22%,有望为中国石油21套装置提供自主技术,降低企业采购成本。
●连续重整催化剂:自主研发的高活性、高芳产连续重整催化剂PCR-01,首次在芳烃型连续重整装置上成功应用,实现中国石油攻克最后一个炼油系列催化剂品种,标志着中国石油掌握炼油催化剂全系列开发技术。
自主创新技术 覆盖65%以上化工过程
保持乙烯裂解馏分加氢、合成橡胶生产等技术优势,在聚烯烃、α-烯烃单体生产技术方面取得突破,为中国石油高端化工新产品开发提供自主技术支持。
●乙烯裂解馏分系列加氢催化剂:开发了乙烯裂解C2~C9馏分段全系列加氢催化剂,在40余套装置推广应用。其中,裂解汽油一段加氢催化剂国内市场占有率超40%,二段加氢催化剂超70%,二段还在俄罗斯SIBUR公司成功应用。
●α-烯烃成套技术:1-己烯成套技术在大庆、独山子石化分别建成工业生产装置,乙烯齐聚生产1-丁烯/1-己烯成套技术应用于国家示范工程项目。今年8月30日,“辛烯等α-烯烃合成成套技术”工业试验装置顺利中交,打破国外垄断地位,填补国内空白。
●合成橡胶成套技术:牵头承担国家重点项目“高性能合成橡胶产业化关键技术”,开发了10万吨/年环保型乳聚丁苯橡胶、5万吨/年丁腈橡胶等成套技术,以及乳聚丁苯橡胶无磷聚合技术、溶聚丁苯橡胶加工应用技术,内部市场占有率67%。
●气相醛加氢催化剂:主要用于丁醛、辛烯醛加氢制备丁醇、辛醇,产品质量达到国标优级品标准,催化剂性能达到国际先进水平,能够替代进口催化剂,实现气相醛加氢催化剂的国产化,已在10余套装置推广应用。
●航空生物燃料生产成套技术:开发出“转化—络合—吸附”毛油精炼工艺,研制了高水热稳定性的油脂加氢脱氧催化剂、表面酸性调控的选择性裂化异构催化剂,编制了原料精炼、加氢脱氧和裂化异构全流程6万吨/年航空生物燃料工艺包,具备工业示范应用条件。
●聚丙烯熔喷料、熔喷布生产技术:攻克产品黄变、气味控制等技术难题,开发出低气味、低VOC降解法熔喷聚丙烯生产技术,建成中国石油第一条熔喷布生产线,助力集团公司打通“熔喷料—熔喷布—医用口罩”全产业链。
●丙烯氧化制备丙烯醛、丙烯酸催化剂:在丙烯原料满足丙烯含量≥99%、硫含量≤50ppm的原料条件下,丙烯转化率≥98.0%,丙烯酸收率≥88.0摩尔百分比,适用于以丙烯为原料,在两段串列的列管式固定床反应器中氧化生产丙烯醛、丙烯酸,先后在10套万吨级装置应用。
●碳四烃中分离异丁烯成套技术:适用于生产叔丁醇产品和生产丁基橡胶、聚异丁烯和甲基丙烯酸酯,碳四烃中异丁烯催化逆流水合制叔丁醇工艺技术已在国内建成4套工业生产装置,完成工艺包编制。
●天然气一段转化催化剂:适用于以天然气为原料的合成氨、甲醇、制氢等装置的天然气一段转化工段,催化剂使用寿命大于36个月,已实现工业应用,转化气甲烷含量较原催化剂降低0.5个百分点以上。
清洁生产技术为绿色生产提供技术保障
●环保型超重力液化气深度脱硫(LDS)成套技术:攻克“液化气脱硫不排碱渣”的难题,已在9套装置推广应用,创效1.26亿元,实现液化气碱渣零排放。自主研发的首套1000吨/年超重力硫酸烷基化示范装置今年7月一次开车成功,为万吨级工业应用奠定基础。
●催化裂化烟气和工艺尾气SCR系列脱硝技术:达到国际领先水平,已在20余套装置应用,内部市场占有率达50%,节省催化剂投资40%,实现乙烷裂解炉脱销首次应用。
●丁苯橡胶废水处理技术:开发出同步去除COD、总磷的催化氧化技术,已分别在吉林和抚顺石化建成乳聚丁苯橡胶含磷废水处理工业装置,年减排COD约880吨、总磷约145吨,确保污水处理厂外排污水全面稳定达标排放。
●VOC预处理技术:开发出可降解的微乳液吸收预处理成套技术,对废气中非甲烷总烃、苯、甲苯和二甲苯的吸收率大于60%,硫化氢去除率大于98%,可与现有废气生物处理装置有机结合,实现污水场外排废气稳定达标排放。已建成工业化装置,年减排VOCs210吨。
化工新产品开发和技术服务助力提质增效
持续完善“产销研用管”五位一体的协同创新模式,建立5个技术服务站,配合企业开发120余个化工新产品,累计产量300余万吨,创效10亿元以上。
●自主聚烯烃催化剂开发新产品:形成了14种聚烯烃催化剂技术,其中7种催化剂分别在抚顺石化、大连石化等10余家公司完成工业应用试验,开发的高性能聚烯烃系列产品可用于注塑、薄膜、纤维、管材等主要领域,总体达到国内先进水平。
●茂金属聚烯烃新产品:成功开发了透明茂金属聚丙烯催化剂PMP-01和超高熔体流动性茂金属聚丙烯催化剂PMP-02,完成工业应用试验,开发了MPP6002等产品,这些产品可用于医用3D打印材料、高透明流延膜和人工关节的开发,标志着中国石油在医用高端聚烯烃材料领域取得了重大突破。
●大中空容器聚乙烯专用料:和抚顺石化合作,在国内率先开发出钛系大中空容器聚乙烯专用料,已生产1400多吨,获得授权发明专利15项,并获得了日本、德国和英国的发明专利授权。
●管材、车用、纤维料等高性能聚烯烃产品:成功开发出 65个牌号180万吨聚烯烃新产品,在聚乙烯管材料、瓶盖料、聚丙烯医用料、低气味车用料、高熔指聚丙烯纤维料等产品开发方面取得了显著成效,形成HPP1850、DQDN3712等一批拳头产品,提升了中国石油产品的市场竞争力。
分析检测与流程模拟优化加快新技术开发应用
●重油四组分快速分析技术:引入最新中压液相色谱技术,除溶样和称量外,再无手动操作。全自动样品分析仅用时120分钟,可同时分析4个样品。系统内置所有运行参数,样品分析一键运行。
●炼化过程模拟优化与装置诊断技术:分子炼油过程模拟技术取得进展,装置与全厂加工方案优化、原油数据库和油品调和技术、反应器流场模拟计算等技术在7家企业应用。汽油加氢示范装置专家诊断系统首次建立炼化专家诊断平台,提高对炼化企业服务支持效率和水平,挖掘技术应用潜力和装置运行效益,为企业提质增效提供支撑。
建院以来,集团公司不断强化对炼化技术的投入和支持,集团公司领导和股份公司管理层高度重视和关心石化院的发展,为石化院高质量发展进一步指明方向。总部科技管理部等部门、炼油与化工分公司等专业公司给予的大力支持,推进了石化院科研工作高起点、高水平、高效率开展攻关与实施。
征途漫漫,唯有奋斗。进入新时代,石化院将始终牢记“支撑当前、引领未来”的征途和使命,坚定贯彻新发展理念,弘扬石油精神,凝聚奋斗伟力,吹响新能源新材料进军号,奏响炼化科技自立自强的时代强音,为建设世界一流研究院不懈奋斗,为世界一流综合性国际能源公司建设做出新的更大贡献!
建院以来,共申请发明专利2485项,已授权1617项。2011年起,发明专利申请和授权量逐年提高,2016年后的授权率为70%,特别是“十三五”时期,发明数量和质量显著提升。2020年专有技术许可取得突破,全院技术许可收入创历史新高,较2019年增加77%,是“十三五”初期的4倍多。
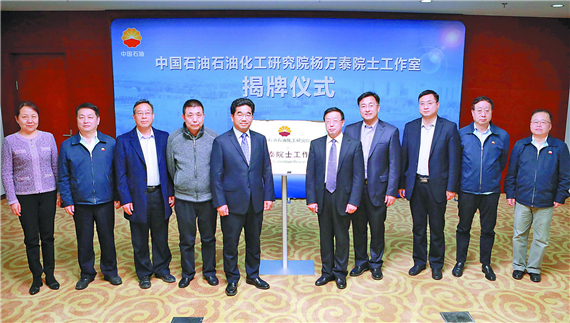
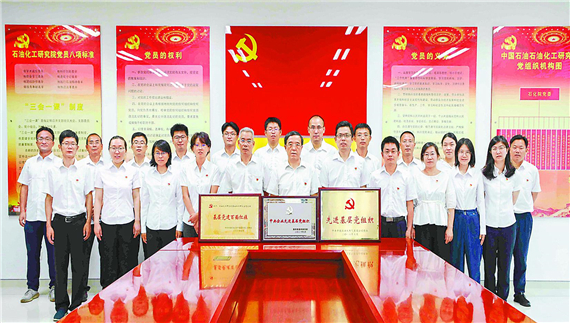
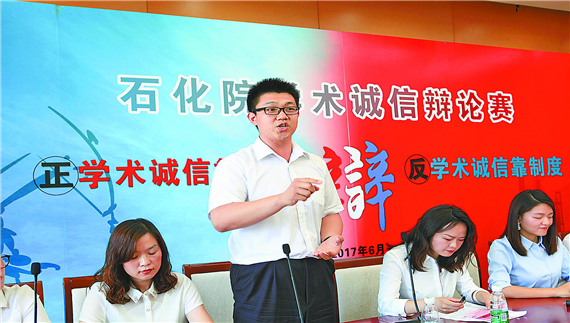